Our equipment
- TOP
- Our equipment
Cutting-edge equipment for high-quality recycling
At West Japan Glass Recycle Center, we have accurate and reliable operating systems in place, making use of a range of cutting-edge equipment in order to deliver high-quality recycling.
By using the latest equipment, we are also able to fully strip the PVB interlayer from automotive and building glass, some of which would formerly have gone into landfill, and recycle it into glass and plastic raw material.
Crushing & sorting lineProcessing capacity: 344 t/day
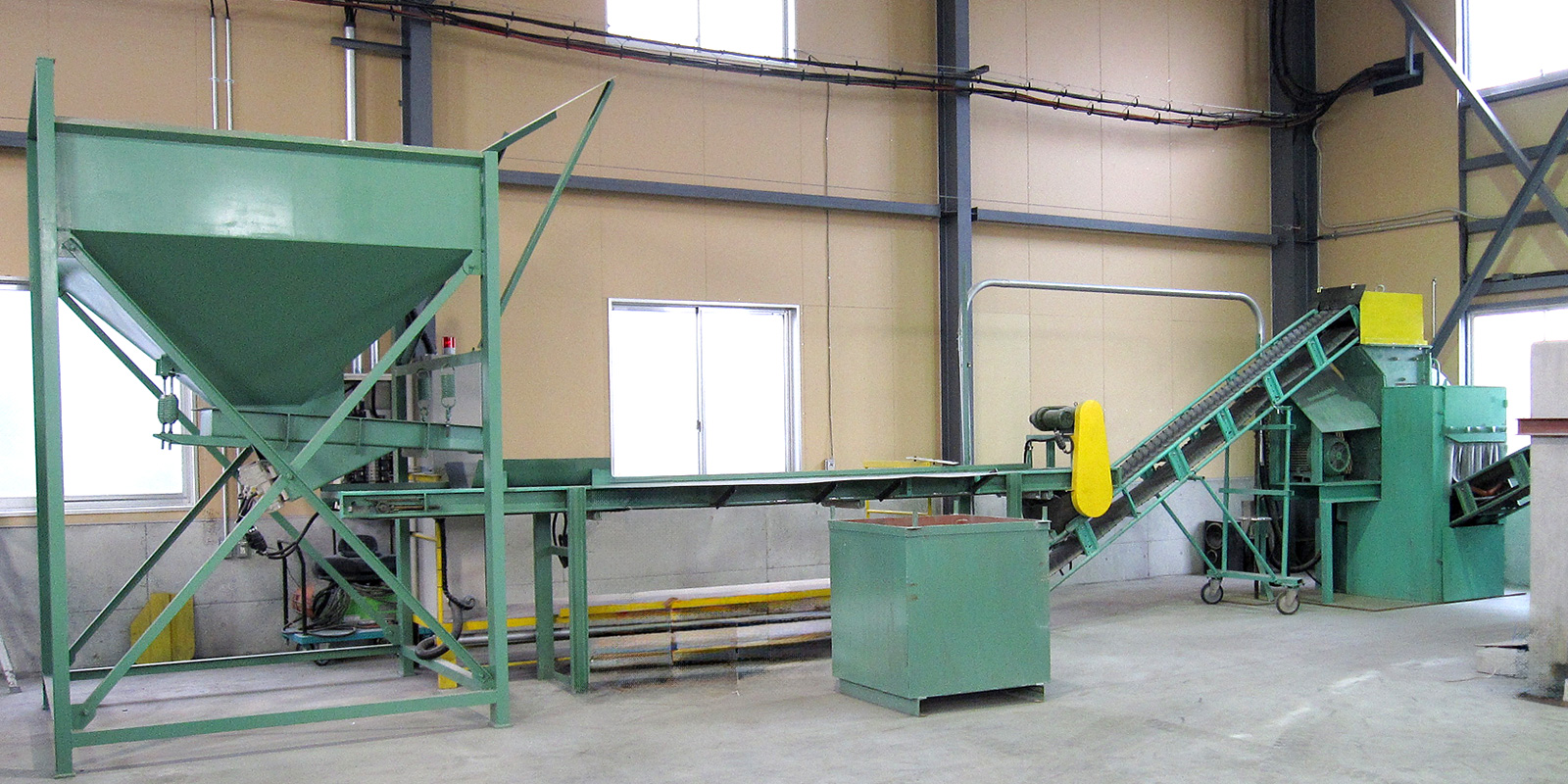
This line is where we separate glass and extraneous materials by hand.
It is mainly used for crushing and sorting hardened glass and glass from fluorescent tubes, but also processes other kinds which require primary sorting by hand due to the presence of high quantities of extraneous material, such as bottle caps, etc.
- Features
-
- Output rate and sorting line speed can be adjusted in accordance with the relative quantity of extraneous material and fragment size.
- The conveyor is movable so can also be used as a sorting line only.
- The crusher uses a special process and a hammer impeller to pulverize without difficulty.
- In particular, wired glass can be processed by separating the crushed glass from the wire enabling the metal to be sold on as scrap.
Return type crushing & sorting lineProcessing capacity: 144 t/day
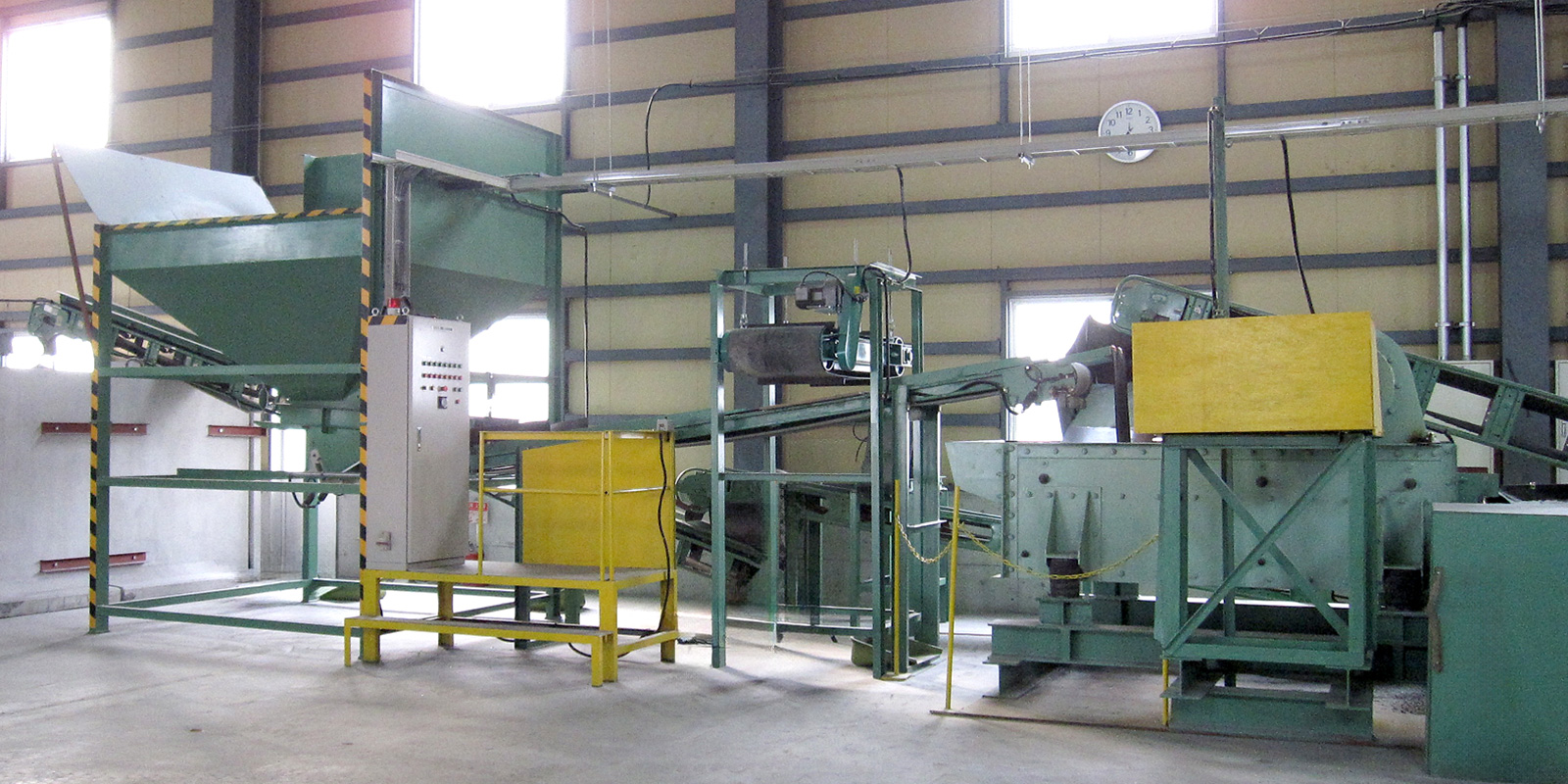
This equipment forms our main line and more than 60% of our product is produced here.
It sorts and crushes our main raw materials, automotive glass, flat glass and bottle glass, on a return system.
It can be in operation for longer than a batch system and enables fully automated processing from input to output.
- Features
-
- Fully automated after input.
- Particle size can be adjusted in advance to avoid crushing more than necessary, improving productivity.
- Special feature of the machine means only glass is finely crushed, while lighter materials such as plastic are not.
- Crushing lines are usually one-way, so using a return system increases efficiency. Further, forcible expulsion means downtime is reduced, improving productivity and glass retrieval rate. In addition, full automation allows continuous operation and greater production than batch systems.
Hammer type crushing & sorting lineProcessing capacity: 33.6 t/day
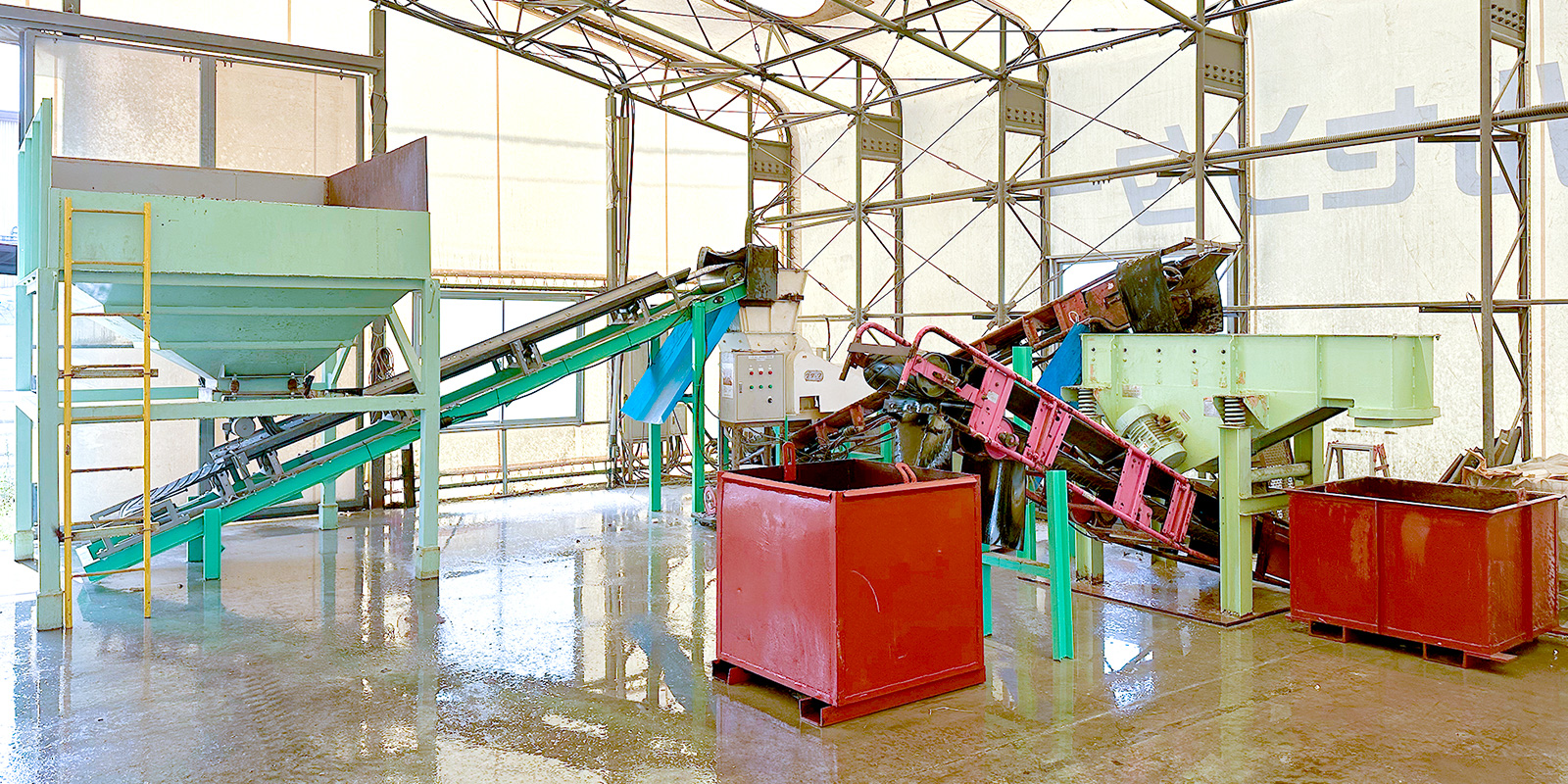
This line processes hardened glass, slag, grindstone, brick, etc.
Using a hammer system enables crushing of harder and larger items.
- Features
-
- Semi-automated.
- Can crush uniformly, regardless of size and shape of items.
- Return system enables comparatively easy adjustment of particle size.
- The hammer crusher’s design enables easy repair and switching of items to be crushed.
Wet agitation and stripping lineProcessing capacity: 19.2 t/day
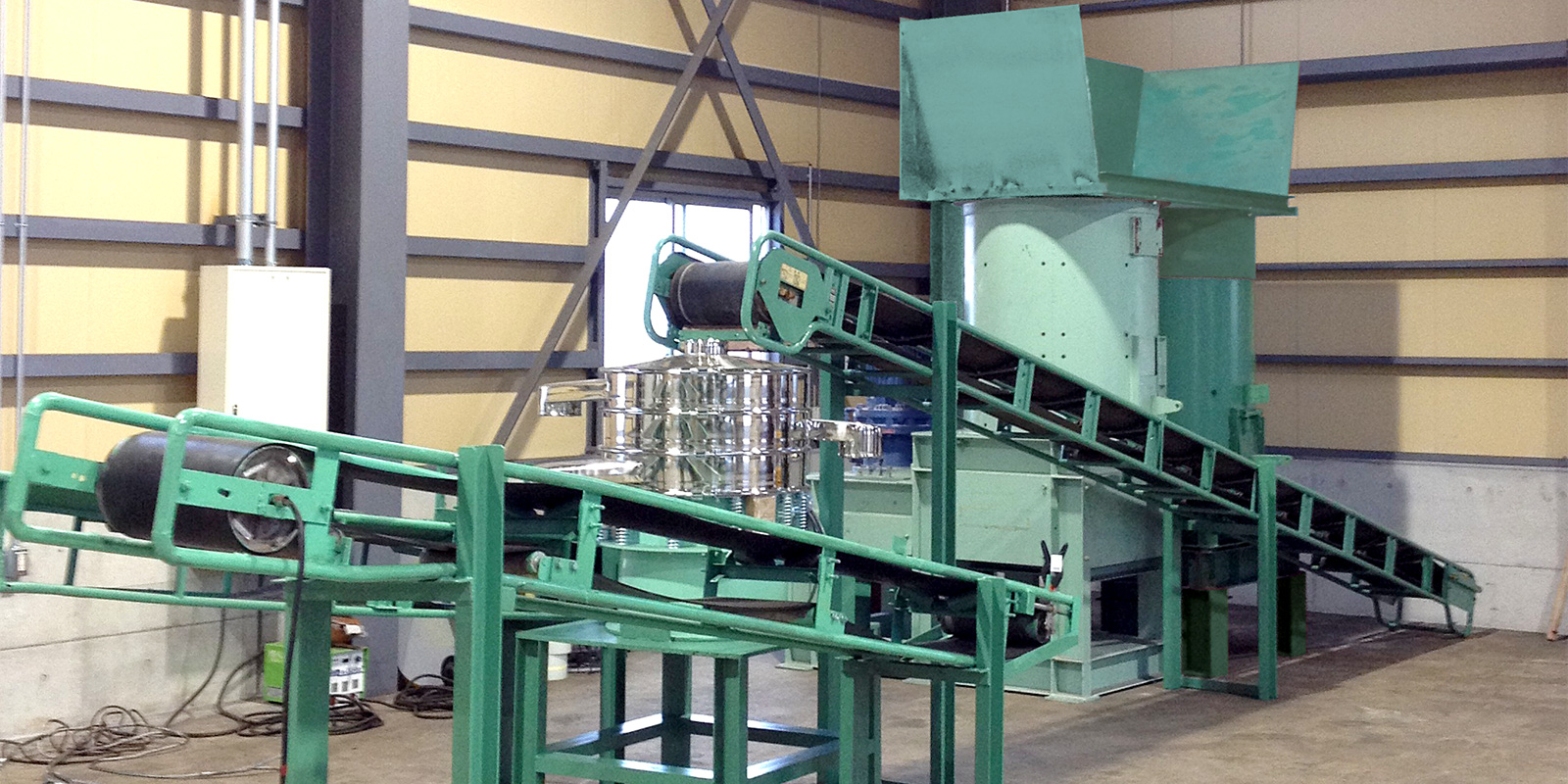
This line strips coatings and film that have been attached to glass.
It can agitate and strip mainly glass that has been coated, such as primer bottles and mirror glass, and glass that has film attached, such as LCD TV screens. Iimuro Glass Ltd. has a patent pending on this special machine, which is one of very few in Japan.
- Features
-
- Removes coating from surface of glass using a specially designed agitator.
- Can also process broken glass, which normal grinders cannot.
- Fully-automated production after input.
- Works on a batch system and can produce a large quantity per operation (2 t/batch)
Optical sorting line (CeraPick master)Maximum processing capacity: 5 t/hour
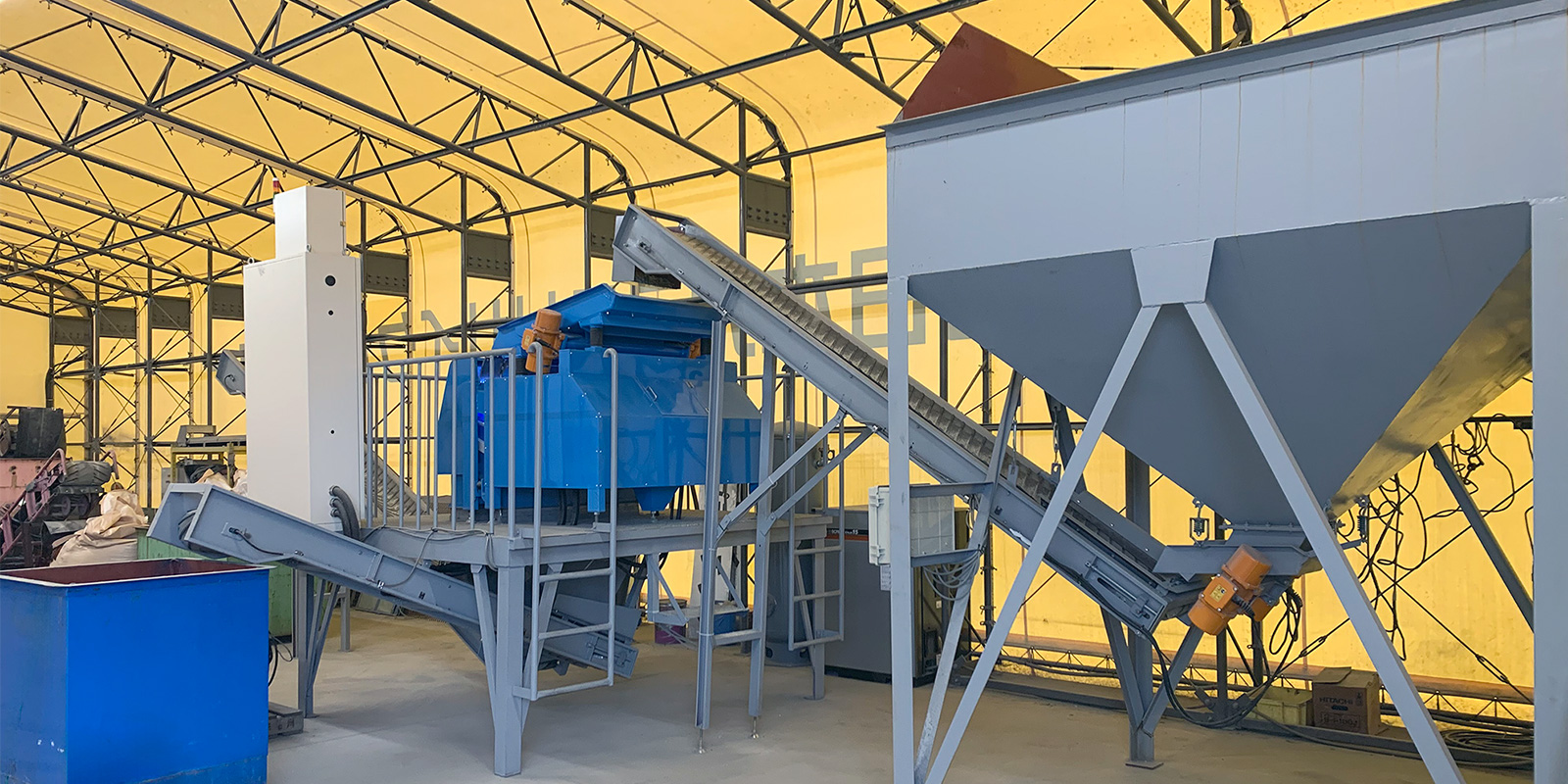
This line uses an optical camera to detect and automatically remove extraneous material.
It can remove even small items, such as pebbles, that would be missed by manual sorting.
As the sorting is done mechanically, it can continually produce cullet of a consistent size.
- Features
-
- Cullet size: 2 mm – 30 mm
- Extraneous material removal rate: 95%
- Uses an optical camera to measure light transmittance of cullet to detect non-cullet material.
- Extraneous material is removed using pneumatic separation as it falls onto the conveyor belt from the machine.
- Margin of error from detection to pneumatic separation is less than 1/100 second.
- Cullet size is easily altered allowing various types of glass material to be handled.